This website uses cookies so that we can provide you with the best user experience possible. Cookie information is stored in your browser and performs functions such as recognising you when you return to our website and helping our team to understand which sections of the website you find most interesting and useful.
NFPA 1971:2018
Minimum Design, Performance, Testing, and Certification Requirements for Structural Fire Protection Ensembles and Ensemble Items Including Pants, Coveralls, Hard Hats, Gloves, Footwear, and Interface Components
This standard does NOT specify requirements for protection against CBRN terrorist agents (chemical substances, biological agents, radiological particles)
The purpose is to establish minimum levels of protection for firefighting personnel assigned to spaces in fire department (proximity or structural fire), rescue, emergency medical, and other first aid functions.
It will provide limited levels of protection against pathogenic, thermal, physical, environmental, and bloodborne hazards encountered during structural firefighting operations. In turn, it establishes the requirements for limited protection against thermal exposures with high levels of radiant heat, convective and conductive heat, and physical exposure; also, to the exposure of contaminating liquids and particles.
All individual items in the protective ensemble that are labeled as conforming to this standard by an accredited laboratory must undergo annual recertification.
All entities (manufacturer, manufacturing plant, product control, quality assurance, compliant product guarantee and marketer) must be accredited by the registered ISO 9001 Quality System.
Each element of the protection set must have at least 1 label located permanently and visibly printed at least in English. The name of the manufacturer, its address, the country of manufacture and the identification number of the element with lot number will be reported. or series as well as the year and month of manufacture; model number or design name and cleaning precautions.
An outer layer, a moisture barrier, and a composite thermal barrier shall be permitted as a single layer or multiple layers.
Garments shall have a means of securing the moisture barrier and thermal barrier to the outer shell.
Closure systems (jacket, pant fly) should be constructed to provide continuous moisture and thermal protection. The clothing must be made with inherently flame resistant sewing thread (melting temperature >= 260ºC (500ºF).
- Burst: Samples conditioned 10 cycles, test according to ASTM D6797
- Seam Resistance: 5 samples in straight seams. test per ASTM D1683 at speed 304.8mm/min (12 in/min)
- Test of Resistance to Water Absorption: 3 samples; test according to AATCC 42 500ml volume of water at 27ºC +/-1ºC (80ºF +/- 2ºF) to be poured over the sample. The % water absorption PWA is calculated
- Water Penetration Resistance Test: 5 samples; test according to Method 5512 (25psi)
- Test of Resistance to Liquid Penetration: test on textile and on seam. 3 samples conditioned at 70ºF (21ºC +/-3ºC) and 65% +/-5% relative humidity for 4 hours. Test according to ASTM F903
- Each fluid should be tested separately against each test sample: AFFF 3% Aqueous Film Forming Foam, Battery Acid 37%, Phosphate Ester Base Fire Resistant Hydraulic Fluid containing 50-80% Tri-Isobutyl Phosphate, Gasoline Substitute (ASTM D471), Pool Chlorination Chemical min 65% Free Chlorine, Automotive Antifreeze Fluid (ethylene glycol 90%) Normal exterior surface of material should be exposed to fluid depending on garment orientation.
- Test of resistance to viral penetration. 3 samples according to ASTM F1671
- Label washing durability test. The sample will be subjected to 10 washing and drying cycles according to AATCC 135 machine cycle 1 washing temperature V drying Ai, load 1.8kgs+/- 0.1Kg. The samples are examined to determine their readability 20/20 at a distance of 30.5mm in a well-lit area.
- Label abrasion durability test. ASTM D4966. The samples are examined to determine their readability 20/20 at a distance of 30.5mm in a well-lit area.
- Convective heat durability test. The samples are examined to determine their readability 20/20 at a distance of 30.5mm in a well-lit area.
- Test fluorescent color requirements (yellow, orange, red)
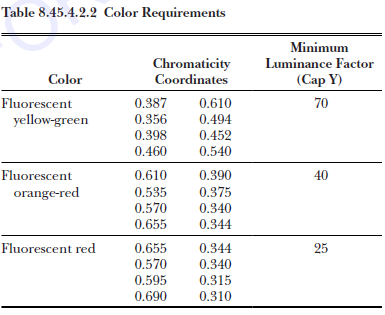
- Test of penetration of liquids in sets and complete garments; Applicable to protective garments, interface gowns, garments, gloves or pants with integrated booties or complete sets.
- 3 complete outfits fitted to the mannequin (chest, waist and crotch height measurements) were tested. Test according to ASTM F1359 with surface tension of water of 35 dynes/cm +/-8; mannequin upright, arms and legs straight. Procedure B: 10 min with 2.5 min in each of the 4 orientations. One of the 3 samples will be allowed to show leakage on the garment in an area not exceeding 20cm2 (3.1in).
- Breaking Resistance Test: 10 cycles ASTM D5034
- Conductive and compressive thermal resistance test: representative composite samples of all layers of the shoulder areas and knees used in the garment. 6 samples of each wet. test according to ASTM F1060 at 280ºC+/-3ºC(536ºF) t0: sensor and sample in direct contact with the exposure surface.
- Determine the time until a 2nd degree burn >= 25 seconds.
- Wet Flexural Test; applicable on outer garment shell materials, 5 samples that were immersed in water at 60ºC +/-3ºC (140ºF) for 15 minutes. After placing the wet samples between blotting papers, a 4.5 kg (10lb) weight, 75mm diameter, 125mm long steel bar is rolled over the sample for four cycles, 8 passes. The sample is placed in the bending device at a tension of 13.5N to 15.75N.
- Low temperature flex test for outer garment shell materials, 5 samples. 4 hour conditioning at -32ºCF (-25ºF). The sample is placed on a template that closes in less than 3 seconds so that it folds face out.
- High temperature block resistance test for the materials of the outer shell of the garment according to Method 5872
- Test for resistance to degradation by light. The samples will be subjected to 40 hours of continuous light. they will be removed and conditioned at 21ºC +/-3 (70ºF) and 65% +/- 5% relative humidity for 4 hours.
- Particle internal leakage test applicable to protection assemblies against liquids and particles; 3 samples. The test will be carried out in a sufficiently large chamber with a stable airflow directed at the test subject. The aerosol used will be a combination of silica 50% tetraethylene glycol 42% 6 & Tinopal. Visual inspection with black light with a wavelength of 365nm. A 35mm camera or equivalent is used to photograph under ultraviolet light before and after aerosol exposure.
- Test of transmitted and stored thermal energy applicable to the sleeves of garments. Test according to F2731 with exposure time of 120 seconds. Time to 2nd degree burn will be calculated
- Flame resistance test according to ASTM D6413M, vertical test in original state and after 5 washing cycles. We evaluated the ability to self-extinguish the applied flame for 12 seconds once removed. The char length of the material after exposure to the flame is also measured. Compounds are individually tested. We observe and record the ease of ignition and char characteristics. This length cannot exceed 100mm and cannot show residual flame 2 seconds after removal and cannot be melted.
- Test for resistance to heat and thermal shrinkage according to ISO 17493. Test on original and after 5 pretreatment cycles. The fabric is exposed to 5 minutes of heat in a 260°C (500°F) oven. The thermal contraction of the fabric after being exposed to high temperatures is evaluated. A contraction > 10% will not be valid. Excessive shrinkage could compromise the firefighter’s mobility and affect the insulating qualities of the garment.
- Tear resistance test for outer layers and collar lining according to ASTM D5587 by trapezoidal procedure in original and after 5 wash cycles. The test measures the force (in pounds) required to continue an existing tear.
- Seam breaking strength test according to ASTM D1683 after conditioning. The size of the test tubes is 50mmx200mm with the seam dividing the length in two until the test tube breaks.
- Viral Penetration Resistance Test per ASTM F1671M for Bloodborne Pathogen Protection using Phi-X-174. Evaluates the ability of moisture barrier fabric and seams to prevent pathogens from coming into contact with the firefighter. The passage of the virus is evaluated after 1 hour. Any evidence of passage of virus through the tissue constitutes a failure.
- Corrosion resistance test according to ASTM B1/7. It is applied to the metal fasteners of the garment in a saline spray for 20 hours. Afterwards the metal may only show slight corrosion on its surface and the hardware must still be functional.
- Total Heat Loss (THL) test per ASTM F1868, garment conditioning compound on a sweating hot plate to assess heat transfer in humid conditions and thermal resistance in dry conditions. These values are combined in an equation to provide a total heat loss value. Higher values indicate better performance and lower values indicate heat loss.